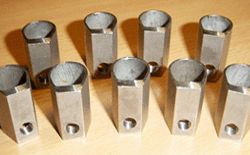
Custom Metal Casting Services
Metal casting is the process in which molten metal is poured into a hollow cavity mold and later cooled to form a solidified part. Casting is ideal for creating detailed parts that meet exacting specifications. Depending on the method you choose, metal casting can allow for a very high production rate with little secondary machining required. Our domestic and global partners work with all types of metals to produce castings using methods such as die casting, investment casting, permanent mold casting, and sand casting.
Compass & Anvil has been a leader in global sourcing for over 30 years. We can help your company eliminate common challenges associated with production, including excessive freight costs, communication barriers with offshore manufacturers, material identification, scheduling, and more. Receive hands-on facilitation throughout the entire product development process to ensure all your needs are met. Check out our customer testimonials to see what others have to say about our service. Contact us today to begin discussing your project needs.
Custom Casting Considerations
Factors to consider for casting services include:
- Quantity of parts/production run size
- Tooling factors into time and cost for production runs. Advantages and disadvantages for each casting method can make choosing the best type of casting process difficult
- Determining your production run size can help connect you with the right foundry. Foundries often specialize in high-volume or low-volume production projects
- Custom requirements and industry standards
- Let us connect you with casting manufacturers who understand industry standards and compliance for your casting application
- Casting design
- Work with vetted casting manufacturers who have the knowledge and expertise to design a custom casting that meets your specifications (with a cost-effective casting mold).
- Casting material
- The type of material you choose for your casting project will depend on your project requirements
- Common materials used for metal castings include aluminum, steel, stainless steel, copper, zinc, magnesium, nickel, and a wide range of alloys
- We can connect you with a manufacturer to meet all your material requirements
Precision Metal Casting Methods
There are several methods for molding metal through casting. The method you choose depends on the volume, complexity, and cost goals of your project. Compass & Anvil can help accelerate your production process by connecting you with a manufacturer who provides the right type of casting for your project, along with a full complement of finishing services, such as drilling holes, painting, polishing, and buffing.
Die Casting
Die casting is a four-step process that involves forcing molten metal under high pressure into a mold cavity, resulting in an accurate and highly repeatable casting method.
Investment Casting
Investment casting is one of the oldest known metal-forming methods. In this process, the mold is formed around a wax pattern that is burned away when the molten metal is poured in.
Permanent Mold Casting
Permanent mold casting uses reusable graphite molds that are ideal for manufacturing high-precision components. Because they can withstand indefinite use, graphite molds can produce castings with accuracy, again and again.
Sand Casting
There are several types of sand casting, including green sand casting, skin-dried sand casting, dry sand casting and no-bake sand casting. Each of these options offers a different set of advantages.
Metal Casting Process Comparison Chart
Die Casting |
Investment Casting |
Permanent Mold Casting |
Sand Casting | |
---|---|---|---|---|
Strength | Good | Good | Highest | Good |
Design Complexity | Fair | Highest | Fair | Fair to Good |
Size Limitation | Good | Fair | Good | Highest |
Pressure Tightness | Fair | Good | Highest | Good |
Reproducibility | Highest | Good | Good | Fair |
Structural Density | Fair | Good | Highest | Good |
Relative Cost | Low | Average | Low | Low |
Rate of Production | Highest | Low | Good | Fair |
Surface Finish | Highest | Highest | Good | Fair |
Tooling Lead Time | Good | Good | Good | Highest |
Tolerances | Highest | Highest | Good | Fair |
Alloy Range | Fair | Good | Good | Highest |
Mold Cost | Fair | Good | Good | Highest |
Casting Weight Range | 1 oz. - 75 lb. | Less than 1 oz. - 25 lb. | 1 oz. - 100 lb. | Unlimited |
Dimensional Tolerances | ±0.001"/±0.0015" | ±0.010"/±0.020" | ±0.010"/±0.050" | ±0.001"/±0.030" |
Minimum Wall Thickness | 1/32" | 1/16" | 1/8" | 1/10" |
Draft Angle | 1°-5° | 1/4°-1/2° | 2°-4° | 1/4°-1/2° |
Castable Alloys | Al-base is preferred | Most Ferrous/Non-Ferrous Metals | Al-base & Cu-base are preferred | Most Ferrous/Non-Ferrous Metals |
Work with Offshore Casting Manufacturers
If keeping costs low is a high priority for your project, we can help you find an offshore casting manufacturer who can deliver high-quality parts for a fraction of the cost. Vetting can be a time consuming process. Compass & Anvil makes it easy! We’ve developed 30 year relationships with vendors all across China, ensuring our customers are able to keep their production costs low without having compromise on quality. Additional benefits of offshore manufacturing include:
- High volume production runs
- Lower tooling and finishing costs
- Specialized capabilities
- Just-in-time logistics
Work with Casting Manufacturers in the US
If a swift turnaround time and clear communication with the manufacturer is your number one priority, we can find a domestic manufacturer who offers the reliable and design-friendly custom casting services you’re looking for. Depending on your project requirements, we can partner you with vendors who maintain all necessary ISO, medical, automotive, and/or aerospace certifications. Additional benefits of domestic manufacturing include:
- Cross-sell opportunities
- Direct communication with design engineers
- Faster fulfillment times
- Reduced shipping costs
Your Trusted Sourcing Partner for Custom Metal Castings
Get the high-performance metal parts you need with the quality custom metal casting methods you want. Let us connect you with an experienced, vetted casting manufacturer for your next metal casting project. Join the network of companies around the country who rely on Compass & Anvil to find the best casting solution for their business needs. Submit a request today or contact us to begin discussing your project requirements.